To perfection
What determines whether you, as a customer, are satisfied? Is it expectations of quality? Status? Technology? Or is it perhaps the bottom line result that truly matters? In fact, it’s likely not a single factor but rather all of them combined. Ever since we designed our first machine over 50 years ago, we’ve operated under a philosophy of completeness. We understand that when every aspect is considered and no detail is insignificant, we improve. We become stronger. Precision drives innovation. It leads to smarter solutions, community, and a different kind of future for our customers. That’s why we work hard to ensure your satisfaction. To perfection.
Brief about us
Our Organization
Our organization is structured with clear areas of responsibility, encompassing tasks, as well as accountability and authority. From the board to operational and management teams, the ambition is to perform at the highest level.
CEO: Overall operational responsibility and ultimate decision-making authority in strategic and operational company matters.
Marketing: Operational sales, as well as strategic communication and marketing. Also responsible for the entire project during the sales phase. The aftermarket ensures that our customers are provided with service, spare parts, and ensure that their plant operates smoothly with minimal disruptions.
Mechanical Engineering: Design, production, and development of machinery. Handles all mechanical aspects up to manufacturing.


Automation: Control and electrical engineering. Works closely with several subcontractors.
Project Department: Responsible for the project after the contract is finalized. For each project, a project team is formed with personnel from most of our departments, with a project manager as the main responsible party. The project department also handles the procurement for the projects and the service organization, which takes care of the plant together with the customer after the project is completed. The project department also manages the documentation for the projects.
Administration: Responsible for finance, data, and personnel-related matters.
Expertise
Sales Representatives
Has the ability to understand customer needs and offer the right solution.
Quotation Engineers
Turns customers’ various requests into solutions. Done in the form of layouts, technical specifications, and cost estimates.
Project Manager
Is responsible for leading, managing, and planning the project from the contract stage to final inspection.
Automation Technician
Programs PLCs, HMIs, servos, and frequency converters, largely in the TIA Portal. Many programs are simulated and tested in the office before the electrical equipment is tested in the workshop and then delivered to the assembly site. It is the automation technicians who start up, test run, and fine-tune the machines before customer handover.
Mechanical Design Engineers
Constructs using professional tools such as Creo and CoCreates Drafting. Draws and develops machines and equipment at the forefront of technology. Also ensures every mechanical part in the delivery to our customers.
Electrical Design Engineers
Work with Engineering Base as a tool. They investigate and adapt the electrical equipment before designing the electrical drawing. The drawing is then sent to cabinet manufacturers and electrical installers. Our electrical designers then provide support throughout the project.
Service Technicians
Possesses knowledge about all our customers’ facilities. A valuable partner in all stages of the equipment’s lifecycle.
Project model for efficient planning and control
The most important prerequisite for a successful project is that we have been attentive and gained the trust to contribute with our knowledge and experience already in the procurement phase. Therefore, the sales team consists from the start of key personnel in all relevant specialist areas. Before the project starts, the sales team hands over the project and the responsibility for customer contacts to our project group. The core of this group consists in most cases of the same engineers who composed the quotation proposal.
Under the leadership of one of our experienced project managers, the project is driven forward according to a well-developed project model, down to every detail.
The goal is always to equally fulfill all requirements for delivery time and smooth cooperation during the project phase as for promised quality and performance when the facility is fine-tuned and ready.
Experience and specialist knowledge
In designing our project model, we have placed great emphasis on two factors:
- Bemanna organisationen med komplett specialistkompetens och erfarenhet i alla steg.
- Säkerställa ett smidigt samarbete genom tydlig rollfördelning mellan alla inblandade, vilket i sin tur skapar ett smidigt samspel med beställarens projektorganisation.
Our project manager has at their disposal a dedicated team from procurement, design, assembly, and commissioning. This provides us with all the conditions to meet agreements regarding schedules, performance, and the quality of the finished facility.
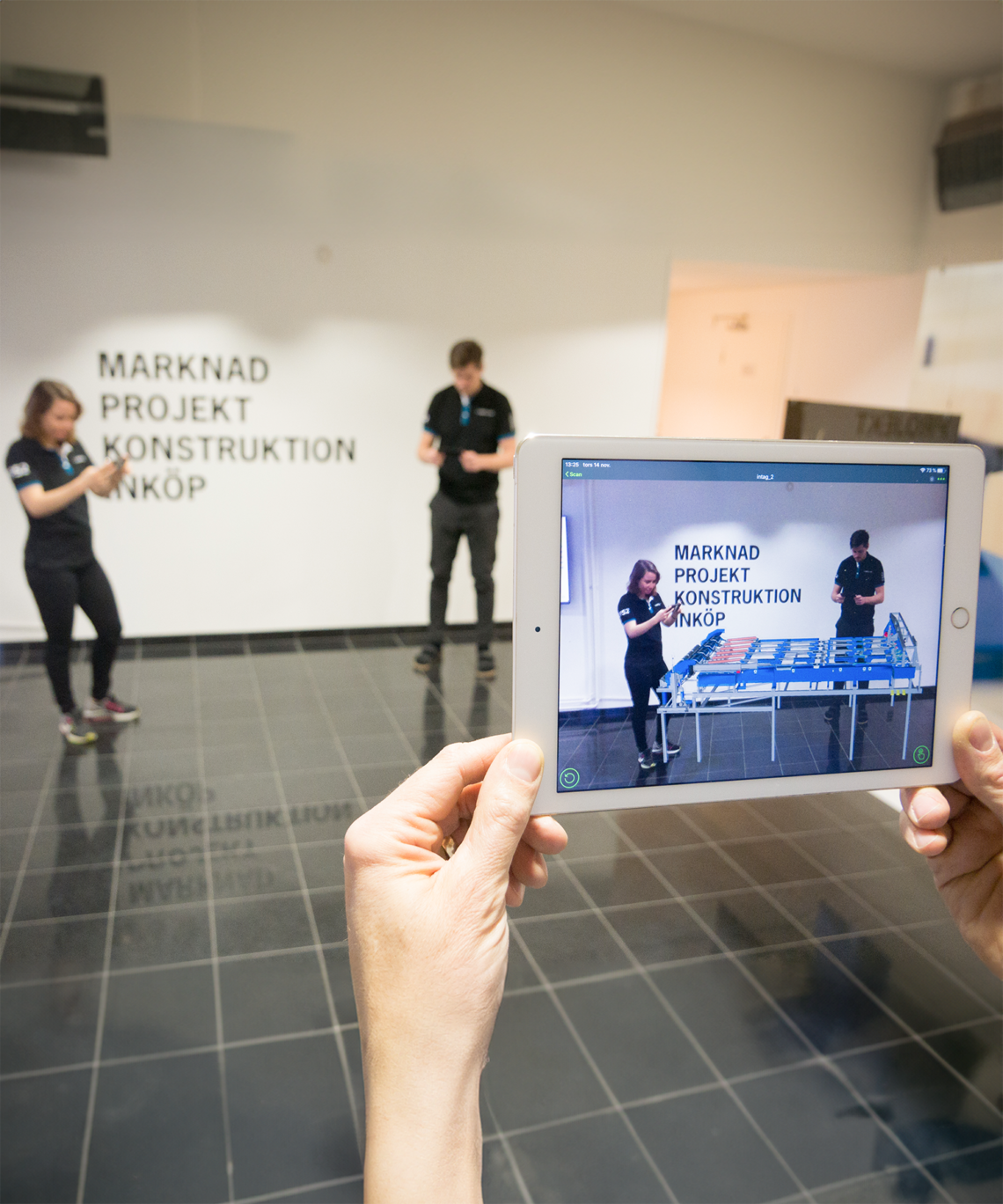
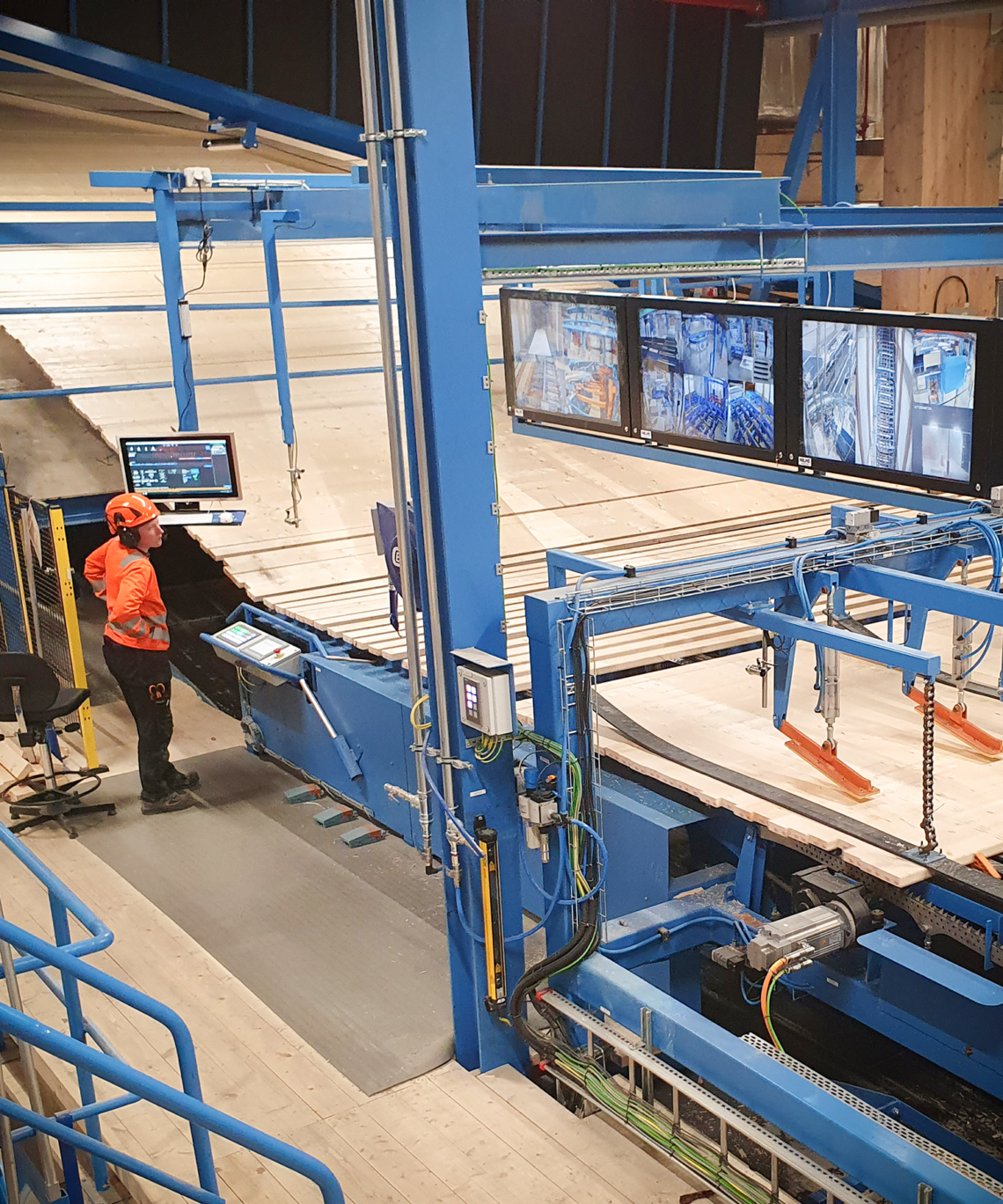
History
Powerful, high-performing, precise, and at the same time of quality you don’t need to replace.
We have our own tradition. That’s why we think about machines differently. Ever since 1972, we have worked according to the principle “best suited and best executed.” Inspiration, ideas, and innovations come from our customers’ diverse needs, our socially skilled engineers, and the opportunities they see together. No shortcuts.
Here you can see the milestones that have shaped us into who we are today:
1952 Renholmen Mechanical Workshop was founded in the village of Renholmen. The main production consisted of hydraulic gear pumps and repairs.
1954 Manufacturing of backhoes for Kewako. Later also for Bröderna Lundbergs.
1960 Manufacturing of loaders for Bröderna Lundbergs.
1962 Hydraulic timber forks begin to be developed and manufactured.
1968 The Hellgren Group buys the company. About 20 employees manufacture timber forks and molds for Skega AB.
1972 The company moves to the newly built factory premises in Byske. Manufacturing and project delivery of sawmill equipment is a new and rapidly growing industry.
1979-80 Competitors Eve Machines and Smedbolaget are acquired by Renholmen.
1985 Contorta buys Renholmen, which at that time has about 150 employees.
1990 Sorb Invest buys Contorta.
1997 Troponor AB, which owns the competitor Hammars, buys Renholmen, which becomes responsible for the timber handling product group within the group. Hammars is closed down and the products are now included in Renholmen’s range.
1999 Carl Bennet becomes the owner and buys Troponor AB, which is merged with Sorb Invest and renamed Sorb Industri AB, a group with over 900 employees and a turnover of approximately SEK 1.1 billion.
2003 Renholmen’s production unit is sold to FeRex AB from Piteå, which takes over the manufacturing. They buy the machinery, take over parts of the staff, and move their entire operations to Byske. Renholmen Mechanical Workshop AB becomes from now on a pure engineering company without its own manufacturing.
2004 Renholmen Mechanical Workshop AB changes its name to Renholmen AB since the company no longer contains any workshop.
2007 Sorb Industri is reorganized into the business area “Sawmill Equipment” within Lifco AB. In total, Lifco has a turnover of just over SEK 5 billion with 2,300 employees.
2010 Renholmen AB and Forslunds Maskin AB merge into a company under the name Renholmen AB, which expands its range to also include timber handling for all kinds of further processing in the wood industry.
2016 Provator acquires Renholmen AB and AriVislanda from the Lifco Group. Almab Storvik AB already belongs to Provator and the three companies are part of a common ownership structure in the company ARA Technology Group AB.
2018/19 Storskogen AB acquires ARA Technology Group AB (ARAT), consisting of Renholmen AB, AriVislanda, and Almab Storvik AB from Provator. During the beginning of 2019, Ingenjörsfirma Gösta Hedlund AB and automation company Milltech were also acquired by ARAT.